本标准等效采用了国际标准ISO 2548-1973(E)《离心泵、混流泵和轴流泵验收试验规范--C级》和ISO 3555-1977(E)《离心泵、混流泵和轴流泵验收试验规范--B级》。 1 主题内容和适用范围 本标准规定了离心泵、混流泵、轴流泵和旋涡泵的流量、扬程、轴功率、转速、汽蚀余量的测试方法及测试数据的处理和误差分析。 本标准适用于以常温清水或性质与常温清水类似的其它液体为试验介质的泵的试验,包括不带任何管路附件的泵和带有管路附件的泵的组合体。 本标准按测量精度分为B级和C级。 2 引用标准 GB 3214 水泵流量的测定方法 GB 1032 三相异步电机试验方法 GB 10890 泵的噪声测量与评价方法 GB 10889 泵的振动测量与评价方法 3 符号 3.1 本标准使用符号 表1 符号
符 号 | 量的名称 | 单 位 | 量 纲 | 符 号 | 中文符号 | m | 质量 | kg | 千克(公斤) | M | L | 长度 | m | 米 | L | t | 时间 | s | 秒 | T | (min,h) | (分,小时) | θ | 温度 | ℃ | 度 | Θ | A | 面积 | m2 | 米2 | L2 | V | 体积 | m3 | 米3 | L3 | ω | 角速度 | rad/s | 弧度/秒 | T-1 | υ | 速度 | m/s | 米/秒 | LT-1 | g | 自由落体加速度 | m/s2 | 米/秒2 | LT-2 | n | 转速 | r/min | 转/分 | T-1 | p | 密度 | kg/m3 | 千克/米3 | ML-3 | Pe | 表压力 | Pa | 帕 | ML-1T-2 | µ | (动力)粘度 | Pa·s | 帕·秒 | ML-1T-1 | v | 运动粘度 | m2/s | 米2/秒 | L2T-1 | P | 功率 | kW | 千瓦 | ML2T-3 | Re | 雷诺数 | - | - | - | D | 直径 | m | 米 | L | q | 质量流量 | kg/s | 千克/秒 | MT-1 | Q | 体积流量 | m3/s | 米3/秒 | L3T-1 | (m3/h,L/s) | (米3/小时,升/秒) | Z | 至基准面的距离 | m | 米 | L | H | 扬程 | m | 米 | L | H1 | 入口总水头 | m | 米 | L | H2 | 出口总水头 | m | 米 | L | T | 比能 | J/kg | 焦/千克 | L2T-1 | Hj1 | 入口水头损失 | m | 米 | L | Hj2 | 出口水头损失 | m | 米 | L | NPSH | 汽蚀余量 | m | 米 | L | Pb | 大气压力(绝对) | Pa | 帕 | ML-1T-2 | Pv | 汽化压力(绝对) | Pa | 帕 | ML-1T-2 | Pa | 泵轴功率 | kW | 千瓦 | ML2T-3 | Pu | 泵输出功率 | kW | 千瓦 | ML2T-3 | Pgt | 原动机输入功率 | kW | 千瓦 | ML2T-3 | η | 泵效率 | - | - | - | K | 型式数 | - | - | - | λ | 摩阻系数 | - | - | - | M | 转矩 | N·m | 牛·米 | ML-2T-2 | W | 重力 | N | 牛 | MLT-2 | 注:带括号的单位不供定义式和计算式使用。 3.2 基本字母和下标(按字母顺序排列) 表2 作符号用的字母 符 号 | 量的名称 | 单 位 | 符 号 | 中文符号 | A | 面 积 | m2 | 米2 | D | 直 径 | m | 米 | g | 自由落体加速度 | m/s2 | 米/秒2 | H | 扬 程 | m | 米 | Hj | 液体水头损失 | m | 米 | K | 型式数 | - | - | k | 绝对粗糙度 | m | 米 | L | 长 度 | m | 米 | m | 质 量 | kg | 千克 | n | 转 速 | r/min | 转/分 | HPSH | 汽蚀余量 | m | 米 | P | 压 力 | Pa | 帕 | P | 功 率 | kW | 千瓦 | q | 质量流量 | kg/s | 千克/秒 | Q | 体积流量 | m3/h | 米3/秒 | (m3/h,L/s) | (米3/小时,升/秒) | Re | 雷诺数 | - | - | t | 时 间 | s | 秒 | (min,h) | (分,小时) | u | 速 度 | m/s | 米/秒 | V | 体积(容积) | m3 | 米3 | X | 容 差 | - | - | Y | 比 能 | J/kg | 焦/千克 | Z | 至基准面的距离 | m | 米 | h | 水银压力计读数 | m | 米 | η | 效 率 | - | - | θ | 温 度 | C | 度 | λ | 摩阻系数 | - | - | μ | (动力)粘度 | Pa·s | 帕·秒 | u | 运动粘度 | m2/s | 米2/秒 | p | 密 度 | kg/m3 | 千克/米3 | ω | 角速度 | rad/s | 弧度/秒 | 注:带括号的单位不供定义式和计算式使用。 表3 作下标用的字母和数字 下 标 | 意 义 | 0 | 规定转速下的值 | 1 | 入 口 | 2 | 出 口 | a | 1)一般:可使用的,有效的;2)与P有关时,接受时 | b | 大气压的 | c | 临 界 | e | 有效的,有用的 | gr | 机组的(总的) | Hg | 水银的 | j | 损 失 | m | 平 均 | sp | 规定的 | u | 有用的 | v | 汽化的 | 4 术语 4.1 一般术语 4.1.1 自由落体加速度g 对C级试验g=9.81m/s2,对B级试验应采用当地的g值。不过多数情况下,取g=9.81m/s2不致有显著的误差。g的当地值可按下式计算: g=9.80617×(1-2.64×10-3cos22ψ+7×10-6cos22ψ)-3.086×10-6Z (1) 式中:ψ——当地的纬度; Z——当地的海拔高度。 4.1.2 转速 n 转数被时间除的商。 4.1.3 密度 P 单位体积的质量。 4.1.4 压力 P 力被面积除的商。除非另有说明,所有压力均指表压力,即相对于大气压力测量的压力。 4.1.5 (动力)粘度 µ 由下式定义: L=µ·uo/h (2) 式中:uo——平板在其自射击的平面内作平行于某一固定平壁运动时的速度; h——平板至固定平壁的距离。但此距离应足够小,使平板与固定平壁间的流体流动是层流; L——平板运动过程中作用在平板单位面积上的流体磨擦力。 4.1.6 运动粘度 u (动力)粘度被密度除的商。 u=µ/p (3) 4.1.7 功率 P 某一时间间隔内所传递的能量被间隔时间除的商。 4.1.8 雷诺数 Re 由下述定义: Re=uD/u (4) 4.2 本标准专用术语 4.2.1 体积流量 Q 单位时间内从泵出口排出并进入管路的液体体积。 4.2.2 质量流量 q 其值为: q=Qp (5) 4.2.3 流速 u 平均流速等于体积流量被管路横截面积除的商: u=Q/A (6) 4.2.4 水头 单位重量液体的能量 4.2.5 基准面 通过由叶轮叶片进口边的外端所描绘的圆的中心的水平面(图1)。 对于多级泵以第一级叶轮为基准。 对于立式双吸泵以上部叶片为基准。 4.2.6 Z 表示所研究的水平面与基准面之间的垂直高差。如果所指的水平面在基准面之上,Z为正值,反之Z为负值。 4.2.7 表压力 Pe 相对于大气压力的有效压力。对应此压力的压力水头力: Pe/pg (7) 如果该压力高于大气压力,其值为正;低于大气压力,其值为负。 图1 基准面 4.2.8 速度水头 单位重量运动液体的动能,用下式表示: u2/2g (8) 式中:u——所研究的截面上的液体平均流速。 4.2.9 总水头 在任何截面处液体的总水头为: Z+P/pg+u2/2g (9) 这是相对大气压力的表达式。绝对总水头为: Z+P/pg+Pb/pg+u2/2g (10) 4.2.10 入口总水头 H1 泵入口截面处液体的总水头为: H1=Z1+P1/p1g+u21/2g (11) 4.2.11 出口总水头 H2 泵出口截面处液体的总水头为: H2=Z2+P2/p2g+u22/2g (12) 4.2.12 泵扬程 H 其值等于泵的出口总水头与入口总水头的代数差。 H=H2-H1 (13) 如果泵输送液体的密度改变不大,则 H=P2-P1/pg+(Z2-Z1)+u22-u21/2g (14) 如果泵输送液体的密度改变显著,则p应以平均值代替: pm=p1+p2/2 (15) 4.2.13 比能 Y 每单位质量液体的能量,由下式确定: Y=gH (16) 4.2.14 入口总水头损失 Hj1 测量点处液体的总水头与泵入口截面处液体的总水头之差。 4.2.15 出口总水头损失 Hj2 泵出口截面处液体的总水头与测量点处的总水头之差。 4.2.16 汽蚀余量 NPSH 入口总水头加上相应于大气压力的水头,减去相应于汽化压力的水头。 NPSH=H1+Pb/pg+Pv/pg (17) 因此,同入口总水头一样,NPSH也与基准面有关。 4.2.17 必需汽蚀余量(NPSH)。 在规定的转速和流量下必需的NPSH值,它由设计制造时给出。 4.2.18 有效汽蚀余量(NPSH)。 在同一流量下有效的NPSH值,它由泵的安装条件确定。 4.2.19 临界汽蚀余量(NPSH)。 通过汽蚀试验测得的NPSH临界值。该临界值是在给定的流量下,在第一级内引起第一级扬程或效率下降(2+k/2)%时的NPSH值;或者在给定的扬程下,在第一级内引起流量或效率下降(2+k/2)%时的NPSH值。 4.2.20 泵输出功率 Pu 泵传递给液体的功率。 Pu=pQgH·10-3 (18) 4.2.21 泵轴功率 Pu 泵轴所接受的功率。 4.2.22 原动机输入功率 Pgr 泵的原动机所接受的功率。 4.2.23 泵的功率 η η=Pu/Pa (19) 4.2.24 机组效率 ηgr ηgr=Pu/Pgr (20) 4.2.25 型式数 K 型式数是一个无因次量,由下式定义: K=2πη (Q')½/60(gH')¾ (21) 式中:Q'——每一吸入口的体积流量; H'——泵的单级扬程。 注:型式数按规定点计算。 4.2.26 规定点 是指对于指定的泵,在设计制造时所给定的转速、流量、扬程、轴功率、汽蚀余量以及效率的值所对应的工况点。 4.2.27 泵工作范围 是指大于和小于规定流量(或扬程)值之间的一定区域。 4.2.28 大流量点 是指泵工作范围内小于规定流量的边界点。 5 试验的实施 5.1 型式检验和出厂检验 形式检验的内容包括:运转试验、性能试验、汽蚀试验以及必要时进行的噪声和振动试验。 出厂试验是对泵工作范围内,包括小流量点、规定流量点、大流量点等三个以上流量点进行试验,检查其扬程和轴功率。在每个流量点下均应测定流量、扬程、轴功率和转速。在开始试验前,应进行试运转试验。试验方法见本标准5.9条。 5.2 试验的组织 精确的测量不仅取决于所使用的测量设备和仪表质量,而且也取决于测试人员的工作素质和技术水平。试验负责人应由在测试技术方面有丰富经验的技术人员担任,一般试验人员应由具备一定的试验专业知识并能够对泵试验进行熟练操作的人员担任。 5.3 试验用的液体 若无特殊规定,试验用常温清水进行。当要求根据常温清水性能预计输送其他液体性能时,其方法应另行规定。 本标准所谓“常温清水”的特性应符合表4的规定。 表4 常温清水的特性 特 性 | 单 位 | 最 大 | 温 度 | ℃ | 40 | 运动粘度 | m2/s | 1.75×10-6 | (质量)密度 | kg/m3 | 1050 | 不溶解于水的固体含量 | kg/m3 | 2.5 | 溶解于水的固体含量 | kg/m3 | 50 | 水中溶解气体和游离气体的总含量(容积): 对于开式回路,不应大于吸水池中温度和压力条件下的气体饱和容积。 对于闭式回路,不应大于吸水罐中温度和压务条件下的气体饱和容积。 5.4 试验设备 所有测试设备均应附有证明其精度符合本标准5.7条要求的报告。精度证明可以通过校准或与其他标准作比较获得。 5.5 试验记录和试验报告 5.5.1 试验记录 试验记录数据要真实、准确。记录单应由试验人员签字。 试验数据的处理和特性曲线的绘制应在试验装置和仪表拆装之前完成,以便对有怀疑的测量结果进行复试。 5.5.2 试验报告 试验报告应由试验负责人审查签字,其内容如下: a.试验的地点和时间; b.制造厂名称、泵名称、型号、产品编号; c.试验性质; d.规定的泵性能参数; e.泵驱动机资料; f.试验设备和测试仪表的名称、型号、规格及精度; g.试验测试数据; h.测试数据的计算和分析; i.试验特性曲线; j.结论。 试验结果与规定值相比较,确定产品性能是否满足由试验性质所要求的规定指标。 5.6 试验装置 5.6.1 标准试验装置 必须采取一切有效措施来保证通过测量截面的液流具有如下特性: a.轴对称的速度分布; b.等静压分布; c.无装置引起的旋涡。 对于C级试验,以上条件是参考条件。 为了保证这些条件,下面对标准试验装置推荐了一些方法。 对于型式数小于或等于1.5的泵可以在标准试验条件下进行试验。 对于型式数大于1.5的泵,这样的试验结果将只适合于规定的条件,而且这种试验的目的在于提供一种保证,即如果安装合适,泵将达到规定的性能。 对于标准试验回路,如图2-4所示,从具有自由液面的水池中引水或是在闭式回路中所设置的具有静止液面的大容器中引水,入口等径直管段长度应是: a.若入口节流阀一直保持全开状态,入口等径直管段长度应不少于7D; b.若入口节流阀处于任意开度状态,入口等径直管段长度应不少于12D。 如果在闭式回路上,在紧接泵的上游处没有静面的大容器,则必须设法保证进入泵的液流无装置引起的旋涡,且具有法向对称的速度分布。 采取下列措施可以避免出现大的旋涡: a.精心设计测量截面上游的试验回路; b.审慎使用整流栅; c.恰当怖置取压孔,使它对测量的影响减至最小。 标准试验装置泵出口等径直管段长度应不小于4D。 图2 卧式泵开式池试验装置示意图 1——试验泵;2——测功计;3——测速仪;4——压力表;5——流量调节阀;6——真空计;7——入口节流阀; 8——水封节流阀;9——水堰;10——流量计;11——换向器;12——量桶 图3 卧式泵开式池试验装置示意图 1——真空表;2——试验泵;3——压力表;4——流量调节阀;5——水堰 图4 卧式泵闭式回路试验装置示意图 1——汽蚀罐;2——水封式闸阀;3——稳定器;4——真空计;5——试验泵;6——扭矩传感器;7——电动机; 8——扭矩转速测量仪;9——压力表;10——流量计;11——流量调节阀 图5 整流栅 5.6.2 如果泵在模拟现场条件下进行试验,则不宜在紧接泵的前面设置整流栅。重要的是模拟回路的液流特性应是可控制的;液流应当尽可能没有装置引起的大的旋涡,并且有对称速度分布。必要时应当用精皮托管排(梳状管)测定进入模拟回路的液流速度分布,以证实液流特性符合要求。如若不然,可以调协象图5的整流栅一类的适当装置来获得要求的液流特性;但是务必注意保证试验条件不受大的不能恢复的压力损失的影响。 5.6.3 同配件一起试验的泵 如果有要求,可将泵同以下配件在一起进行试验: a.在现场实际最终安装的有关配件; b.或与a 完全一样的复制件; c.或为试验目的引入并作为泵本身组成部分的配件。 整个机组的入口侧和出口侧与试验管的连接应按本标准5.6.1条的图2~4方式进行。 此外,测量应按本标准6.2.1.4条进行。 5.6.4 淹没条件下的泵装置 对于泵或泵与配件的组合体,当不能做到如本标准5.6.1条所述的标准管连接时(由于不能接近或淹没之故),其测量应按本标准6.2.1.5条进行。 5.6.5 深井泵 通常,深井泵不可能将其全部扬水管都装上进行试验。对于未装的这部分扬水管的水头损失及传动轴系所消耗的功率均不能测得。而且泵的任一止推轴承在试验时所承受的负载也总比在最终实际安装条件下工作的负载为轻,所以不能测定出最终的功率。 5.6.6 自吸泵 原则上自吸泵的自吸特性应在规定的吸入静水头下并装上与最终实际安装时一样的吸入管路来进行试验。 如果不能按照上述所提出的方式进行试验,则应按另行规定的技术条件试验。 5.7 试验条件 5.7.1 试验的进行 试验的持续时间应足够,以获得一致的结果,这将关系到试验精度。 对于取多次读数以降低误差的场合(见本标准5.7.2条)应在不等的时间间隔下取读数。 所有的测量均应在运转稳定的情况下进行。 5.7.2 运转稳定性 5.7.2.1 对本标准而言,下列定义适用: 波动——在一次读数的时间内,读数相对平均值的短周期变动。 变化——同一量相邻两次读数间的数值改变。 5.7.2.2 允许读数波动及稳定装置的应用 在由泵的运转或结构而导致读数大幅度波动的场合下,可以用一种能提供至少是在全波动周期内读总和平均值的仪器来进行测量。这种仪器的校准应遵守专门条款的规定。 在需要把波动幅度(测定量的平均值)减少到表5的规定范围以内时,可以在测量仪表及其连接管中装设有限的稳定装置(阻尼器)。 表5 最大允许波动幅度 测定量 | 最大允许波动幅度 % | B级 | C级 | 流 量 扬 程 转 矩 功 率 | ±3 | ±6 | 转 速 | ±1 | ±2 | 注:(1)当使用差压计测量流量时观测液柱差的最大允许波动幅度 B级:可定为±6%; C级:可定为±12%; (2)对入口总水头和出口总水头的测量来说,最大允许波动幅度应根据泵的扬程分别计算。 当稳定装置可能对读数精度产生明显影响时,应采用对称的线性稳定装置(例如毛细管)重做试验。 5.7.3 成组观测读数 5.7.3.1 在稳定和调整好的试验条件下,对规定的试验条件只记录各个测定量的一组读数。 这一组读数只有当观测者确信波动已稳定在表5和表6规定的范围以内时方可进行记录。 5.7.3.2 当试验条件下稳定引起对精度产生怀疑时,应按下述方法处理之。 试验点的读数应重复多次,除转速和温度允许调节外,节流阀水位、轴封部分、平衡水等应完全保持不变。同一量的各次重复读数间的差异是衡量试验条件不稳定的一种尺度。这种不稳定性,除了安装因素的影响外,试验中的泵至少也对它产生一部分影响。 对于每个试验点,最低限度应取三组读数,并且应记录每一个独立读数的值,以及由每组读数得出的效率值。每一量的最大值与最小值之间的百分数差应不大于表6的规定。应该注意,如果重复读数次数增至最多9组时,允许允差已较宽。 这此允差用来保证由于离散所致的误差与由表7所限定的系统误差合在一起后的总测量误差将不大于表8的规定值。 取每一量的各次读数的算术平均值作为该量的试验实际值。 如果不能达到表6的规定,则应找出原因,调整试验条件,并重取一组新的读数,亦即原先一组读数应全部作废。但是不应该以读数超出范围为理由,而拒绝读数或从这成组观测值中选择读数。 要是读数变化过大,不是由于操作方法或仪表误差等所致,因而无法加以消除时,误差限可以用统计分析法计算之。 表6 同一量多次重复测量的变化范围(基于95%的置信限) 重复读 数组数 | 每一量重复读数的最大值与最小值间的最大允差 % | 流量 扬程 转矩 功率 | 转速 | B级 | C级 | B级 | C级 | 3 | 0.8 | 1.8 | 0.25 | 1.0 | 5 | 1.6 | 3.5 | 0.5 | 2.0 | 7 | 2.2 | 4.5 | 0.7 | 2.7 | 9 | 2.8 | 5.8 | 0.9 | 3.3 | 注:最大值与最小值之间的百分数差等于: 最大值-最小值/最大值×100% 5.7.4 试验时的转速 试验转速n与规定转速nsp间的差异可用如下百分数表示: n-nsp/nsp×100% (22) 其差应在下列范围内: a.对流量和扬程:转速相差为规定值的+20%~-50%。 b.对泵的效率:转速相差为规定值的±20%。 对电动机一泵整体机组,试验转速和规定转速下的电动机效率改变应另行规定。 c.对汽蚀试验:假定试验时泵的流量在最高效率点流量的(0.5~1.20)范围内,转速相差为±20%。 注:对于符合本标准7.1.1条要求的试验,上述的转速变化总是可以行得通的;对于符合本标准7.1.2条要求的试验,对型式数小于或等于2的泵,这样变化也是可行的;而对于型式数大于2的泵,则应得到有关各方的同意。 5.7.5 扬程的调节 采用同时节流吸入管路和排出管路或节流两者之一的办法以及连同采用其它方法可以得到所需的试验条件。不过,在吸入管路上节流时,对可能发生汽蚀或使水中溶解空气析出这一点必须给予应有的注意,它可能会影响泵的运转(见本标准7.2条)或流量的测量(对节流式流量计),或者同时影响两者。 5.8 测量精度 本试验中规定的测量误差范围是指测得的数据以及由这些数据算出的量的误差范围,它表示测得性能与实际性能之间的最大可能差异。详细的误差分析和计算方法见附录D(补充件)。 本标准规定了测定流量、入口总水头、出口总水头、泵扬程、转速和泵轴功率的标准测量方法及使用的仪表。 凡是经过校准或通过与有关的国家标准相比较,证明基测量误差不超过表7规定范围的任何测试设备或方法均可使用。 表7 测量仪表的允许系统误差 测 定 量 | 允 许 范 围 % | B级 | C级 | 流 量 | ±1.5 | ±2.5 | 泵扬程 泵轴功率 | ±1.0 | 原动机输入功率 (对机组效率试验) | ±2 | 转 速 | ±0.2 | ±1.0 | 如果符合表7所规定的仪表系统误差并遵循本标准的试验方法,则可认为总的误差限将不会超过表8的规定。 表8 最大总误差限 测 定 量 | 允 许 范 围 % | B级 | C级 | 流 量 | ±2.0 | ±3.5 | 泵扬程 泵轴功率 原动机输入功率 (对机组效率试验)±1.5 | | 转 速 | ±0.4 | ±1.8 | 泵效率 | ±2.8 | ±5.0 | 机组效率 | ±2.5 | ±4.5 | 5.9 运转试验 泵应在规定转速及工作范围内工况点进行运转试验,必要时可商定在最终安装现场进行。 运转试验持续时间不得小于表9的规定。 运转试验时应检查泵的轴承和填料的温升,填料函的泄漏及密封、噪声、振动情况。关于泵的密封环、平衡盘、轴承等处磨损情况可在试验完后进行检查。 表9 运转试验持续时间 规定工况下泵的轴功率 kW | 运转试验时间 min | <50 | 30 | 50~100 | 60 | 100~400 | 90 | >400 | 120 | 5.10 性能试验 5.10.1 一般规定 性能试验是为了确定泵的扬程、轴功率、效率与流量之间的关系。试验应从功率最小的工况开始顺次进行。 离心泵的试验最好是从零流量开始。至少要试到大流量点流量的115%。 混流泵、轴流泵和旋涡泵的试验从阀门全开状态开始。至少要试到小流量点流量的85%。 试验应有足够的持续时间,以获得一致的结果和达到预期的试验精度。每测一个流量点应有一定的时间间隔,并应同时测量流量、扬程、转速和轴功率。 5.10.2 试验测量点 测量点应均匀地分布在整个性能曲线上。 离心泵和旋涡泵应取13个以上不同流量点。 混流泵和轴流泵应取15个以上不同流量点。 5.11 汽蚀试验 汽蚀试验是为了确定泵的临界汽蚀余量与流量之间的关系,或者是验证泵的临界汽蚀余量小于或等于规定的必需汽蚀余量值。 决不应当用汽蚀试验来验证泵在其使用期限内不会发生汽蚀损坏。 6 流量、扬程、转速和轴功率测量方法 6.1 流量的测量 流量测定应按GB 3214进行。 6.2 扬程的测量 6.2.1 泵扬程 6.2.1.1 泵的扬程按本标准4.2.12条所下的定义进行计算。 但在有些情况下,泵的扬程可以用一个差压计来直接进行测量。 如认为更合适,泵的扬程可以用泵输送液体的比能增量来表达(Y=gH)见本标准4.2.13条)。 比能的增量可由上述的泵扬程公式两边乘以g得出。 6.2.1.2 入口和出口摩阻损失 泵的扬程是指泵的出口法兰处与入口法兰处的总水头差,而测压点通常离这些法兰还有一段距离。因些,在测得的泵扬程中需将测压点至泵法兰之间由于摩阻所造成的水头损失(Hj1和Hj2)加上。 但是,只有当Hj1+Hj2≥0.002H(对B级),或Hj1+Hj2≥0.05H(对C级)时才需进行这种修正。 如果测压点与法兰之间的管路是等径圆截面无阻碍直管路,则摩阻损失由下式求得: Hj=λ·L/D·u2/2g (23) λ值由下式求得: (24) 式中:Re=uD/u(纯数值)。 k/D=管路粗糙度/管路直径(纯数值)。 附录B(补充件)给出了指导性图表,它可以用来核对是否需要作这种修正和计算修正值(如需修正的话)。 如果管路不是定常圆截面无阻碍直管路,则应另行规定所用的修正方法。 6.2.1.3 合乎本标准5.6.1条的试验装置。如采用弹簧压力计测量出口和入口压力,当入口压力大于大气压力时,如图6a所示,扬程的计算方法如下: H1=P1/pg+Z1+u21/2g (25) H2=P2/pg+Z2+u22/2g (26) H=(P2-P1)/pg+(Z2-Z1)+(u22-u21)/2g (27) 当入口压力小于大气压力,入口测压连接管内充满空气时,如图6b所示,扬程的计算方法如下: H1=P1/pg+Z1+u21/2g (28) H2=P2/pg+Z2+u22/2g (29) H=(P2-P1)/pg+(Z2-Z1)+(u22-u21)/2g (30) 注:在此条件下,P1为负值,因此实际运算时,实测的P1,P2读数(绝对值)应相加,如果P1的读数单位是水银柱高,应按水银压力计计算。 如采用水银压力计测量泵出口压力和入口压力,当入口压力大于大气压力时,如图7a所示,扬程的计算方法如下: H1=PHg/p·h1+Z1+u21/2g (31) H2=PHg/p·h2+Z2+u22/2g (32) H=PHg/p·(h2-h1)+(Z2-Z1)+u22-u21/2g (33) 当入口压力小于大气压力,入口测压连接管内充满空气,如图7b所示,扬程的计算方法如下: H1=PHg/p·h1+Z1+u21/2g (34) H2=PHg/p·h2+Z2+u22/2g (35) H=PHg/p·(h2-h1)+(Z2-Z1)+u22-u21/2g (36) 注:h1——在此情况下,水银柱读为负值,所以实际计算时,实测的h2和h1的读数(绝对值)应相加。 对于低扬程泵,使用一个双管水银压力计测量泵出口和入口压力差,如图8所示,扬程的计算方法如下: H=(PHg-p)/p·h+(u22-u21)/2g (37) 图6 用弹簧压力计测量泵的扬程 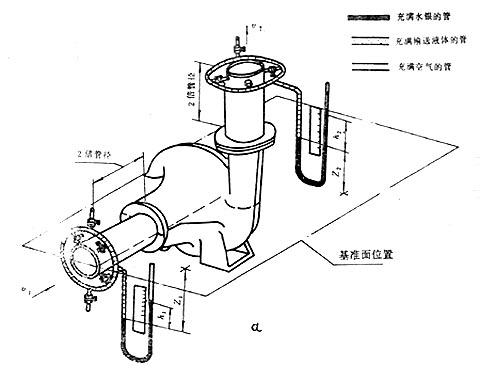 图7 用液柱压力计测量泵的扬程 图8 用一个差压计直接测量泵的扬程 6.2.1.4 当泵与构成现场装置或试验装置一部分的配件合在一起进行试验时,本标准6.2.1.3条中的规定是指配件的入口和出口法兰而不是泵的入口和出口。 这种测量方法就使入口侧和出口侧配件所引起的全部水头损失都归在泵上。 试验时泵应装上与现场最终安装相一致的管路设备。在这种情况下,测量入口压力的截面与入口法兰之间以及测量出口压力的截面与出口法兰之间的管路摩阻损失应按本标准6.2.1.2条所述的方法进行计算,并将其值加到位置水头,压力水头和速度水头三项增量的总和之中。 6.2.1.5 如果在小流量工况泵入口处产生了预旋,则泵入口总水头的测量将会产生误差,其误差的检测和修正见附录C(补充件)。 6.2.1.6 如果泵的入口侧或出口侧不能接近或者两侧都不能接近 ,则泵的扬程测量应按下述方法进行。在某些情况下,如本标准6.2.1.2和6.2.1.4条中提出摩阻损失应予计及。 6.2.1.7 象图9a这类装置的扬程计算应是: H1=Z1 (38) H2=P2/pg+Z2+u22/2g (39) H=P2/pg+Z1.2+u22/2g (40) 如果泵从有压力的静止液面水池中吸水,并向有压力的静止液面水池排出如图9b所示,泵的扬程计算方法如下: H1=P1/pg+Z1 (41) H2=P2/pg+Z2 (42) H=P2-P1/pg+Z1.2 (43) 显然这样的计算就使入口侧和出口侧的配件引起的全部损失都归在泵上。 在这种情况下,摩阻损失可按本标准6.2.1条所给出的方法和附录B(补充件)来确定。 入口摩阻损失主要由入口滤网、底阀以及吸入管中的流动阻力引起。 出口摩阻损失由扬水管和出水弯头中的流动阻力引起。 通常深井泵不装全部扬水管进行试验,在此情况下,制造厂应估算与泵扬程有关的扬水管摩阻损失,并给予说明。 假如需要通过现场试验来核实所标明的数据,则应另行规定。 图9 各种沉没式泵的扬程H的测量 6.2.2 取压孔 6.2.2.1 对于B级,分别在入口和出口管路上沿圆周方向对称地各开设4个取静压孔;取压孔的位置应在离泵的入口法兰2倍入口管径远的上游处和离泵出口法兰2倍出口管径远的下游处。 各取压孔应通过截止阀或旋塞与一环形汇集管连通,环形泄集管的横截面积应不小于全部取压孔横截面积的总和。这样,需要时就可以测量任一取压孔的压力。观测前,应在正常的泵试验条件下逐一分别打开各取压孔,测量各取压孔压力。如果其一读数与4个测量值的算术平均值之差超过总水头的0.5%或者超过测量截面处速度水头一倍时,则应在试验开始前查明读数弥散的原因,并对测量条件进行调整。 注:当同样的取压孔用来测量NPSH值时,此偏差不应超过1%NPSH值或动水头值的一倍。 入口总水头应根据环形汇集管测得的压力水头、测量点的位置水头和速度水头(假定入口管中的流速是均匀的进行计算)来确定。 出口总水头应根据环形汇集管测得的压力水头、测量点的位置水头和速度水头(假定出口管中的流速是均匀的进行计算)来确定。 出口处能量测量的可能误差是由旋涡和局部速度分布不同引起的。 6.2.2.2 对于C级,入口取压孔一般设在与泵入口同心同直径的管路上。正常情况下是设在泵入口法兰上游2倍入口管径处。不应在下列部位设置取压孔: a.扩散管内和扩散管下游4D以内的直管部分; b.弯曲面内,无论弯头本身或弯头下游4D以内的直管部分。但是在此区间,可以垂直于弯曲平面设置取压孔; c.截面急剧缩小部分下游4D以内或者其他形式的截面积突变部分下游4D以内的直管部分。处理非标准条件下的读数结果时应考虑: a.入口水头本身值的重要性如何,如对汽蚀的试验; b.入口速度水头与泵扬程的比例。 如果此比值很小(0.5%以下)或入口水头值不重要,可以把泵入口法兰取压孔的读数代到入口总水头公式(11)中计算。 出口取压孔通常设置在泵出口法兰下游2倍出口管径处。对于型式数小于或等于0.5的泵。如果出口取压孔是在垂直于蜗壳平面或泵壳形成的变终究平面的位置上,即么该孔亦可直接设置在泵的出口法兰上。 对于型式数超过0.5的泵,直平行管必须与泵排出管同心、同直径。在管壁上开取压孔时应位于与蜗壳平面或泵壳形成的弯管平面相垂直,并通过管轴心线的平面内。 6.2.2.3 取压孔应按图10所示的要求制造。孔中心线应垂直于管的内壁面,边缘不得有毛刺,周围光滑齐平。取压孔的直径应为2~6mm或等于取压孔管径的1/10,取两者中的小者,孔深应不小于2.5倍孔径。 取压孔与测压仪表之间的连接管的内径至少应等于取压孔的直径。连接系统要严密不漏。 测压仪表之前应加装三通旋塞阀或者加设有限的阻尼器。这样,当测压仪表的读数剧烈波动时,可进行必要的调整,或者排除连接管中的空气。 图10 取压孔要求 6.2.3 测压仪表 6.2.3.1 液柱压力计 液柱压力计不需要校准。 液柱压力计应避免在液柱差压小于50mm的区间内使用。 液柱压力计引压管径对于水银至少应为6mm。对于水及其他液体至少应为10mm。液柱压力计内的液体必须清洁,以避免由于表面张力的改变而引起误差。 单管或双管水银压力计开端使用测量真空时,应避免连接管内和压力计内充水。 6.2.3.2 弹簧压力计 弹簧压力计的精度应不低于0.4级。 按泵的规定点工况选用弹簧压力计,指针的示值应在压力计量程的1/3以上。 弹簧压力计的读数应当读到测定扬程的1/100。 当测量压力大于大气压力时,应排尽仪表与取压孔之间连接管内的空气并充满水之后再读仪表的示值。 当测量压力小于大气压力时,弹簧直空压力计的连接管内允许充气,但应注意连接管内不得存水。 6.2.3.3 重力压力计 采用重力压力计或活塞压力计(无论是单式还是差动式)来测量超过液柱压力计测量范围的压力是切实可行的。 单式压力计的有效直径de可以取活塞直径dp(直接测得的)和液缸直径dc的算术平均值,如果试验前满足下列条件: dc-dp/dc+dp≤0.1% 则可以用有效直径de来计算压力而不需要再作校准。 由于活塞至少以30r/min的速度作旋转运动,活塞与液缸之间的摩擦力可看作零。 最好是通过与一液柱压力计相比较以确定在尽可能宽的压力范围内的有效活塞直径,来校准重力压力计。 类似的原则也适用于差动式重力压力计。用重力压力计串联液柱压力计或采用有液柱压力计的特殊重力压力计来测量变化的压力亦是有益之策。 6.2.3.4 其他型式压力计 如符合本标准5.8条表7所规定的精度等级,并具备液柱压力计、弹簧压力计或重力压力计功能的其它型式压力计亦可使用。 6.3 转速的测量 转速测量可用直接显示的数字仪表测出测量时间内的转数。 对于交流电动机驱动的泵,可由平均频率观测值和转差率确定。当采用闪光测频法和感应线圈法测定转数和转差率时,可按GB 1032中9.2.2及9.2.3条进行。 6.4 轴功率的测量和效率的计算 泵的轴功率应通过测定转速的扭转力矩得出,或由测量与泵直接连接的已知效率的电动机的输入功率来确定。 6.4.1 扭转力矩的测量 测量扭转力矩可采用天平式测功计和扭转式测功计。测量扭转力矩时应同时测定转速。 按泵的规定点轴功率选用天平式测功计和扭矩传感器,其值应在测功计或扭矩传感器额定值的1/3以上。 6.4.1.1 天平式测功计的重心应位于旋转轴轴心线上。 天平式测功计的不灵敏度可用加最小负荷△来确定。天平式测功计与泵脱离并且电枢旋转时加负荷△使天平的秤盘平衡位置发生移动时的力矩即是不灵敏度。 当天平力臂长等于0.974m时,其不灵敏度不得超过表10的规定。当力臂大于或小于0.974m时,负荷△数值可以成比例地减小或增加。 6.4.1.2 采用天平式测功计测量扭转力矩时,应该用精度等级不低于0.1%的杠杆式天平或带式天平测定作用于臂上的力。 臂长和杠杆长应按误差不超过0.1%计算确定之。 6.4.1.3 扭转式测功计应在扭转轴不承受弯矩的情况下测定扭转力矩。为此,扭转轴与泵和电动机的连接应保证同心。 6.4.1.4 用扭转力矩法计算轴功率 Pa=π/3·Mn10-4 (44) 当用天平式测功计时 M=W·l (45) 式中:l——天平力臂长,m。 表10 不同转速下天平测功计允许不灵敏度极限 N·m 转速 r/min | 500 | 750 | 1000 | 1500 | 3000 | 极限值 | 功率 kW | 7 | - | - | - | 0.0716 | 0.0363 | 10 | - | - | 0.1509 | 0.1051 | 0.0525 | 20 | - | 0.4060 | 0.3104 | 0.2101 | 0.1051 | 50 | 1.6238 | 1.1271 | 1.7642 | 0.5253 | 0.2579 | 100 | 3.1044 | 2.1014 | 1.6238 | 1.1271 | 0.5253 | 200 | 7.4028 | 4.2984 | 3.1044 | 2.1014 | 1.1271 | 300 | 9.5520 | 7.4028 | 4.7760 | 3.1044 | 1.6238 | 6.4.2 电动率的测量 当通过测量与泵直接联接的电动机输入电功率来确定泵的轴功率时,使用的电动机应当是以足够的精度确定其效率的。 交流异步电动机的效率应按GB 1032标准规定的方法进行确定。 6.4.2.1 电动机输入功率的测量按GB 1032标准规定进行,试验应保证使用仪表系统误差满足表7的规定。 仪表的量程选择应使测量值尽可能在仪表额定值的20%~95%范围内。 6.4.2.2 已知电动机效率ηmot的泵轴功率为: Pa=Pgr×ηmot (46) 6.4.3 效率的计算 6.4.3.1 泵的效率 η=Pu/Pa×100% (47) Pu=pQHg10-3 (48) 6.4.3.2 机组效率 ηgr=Pu/Pgr×100% (49) 6.4.3.3 不能完整测得的效率 例如深井泵通常不装全部扬水管进行试验,在这种情况下,泵的止推轴承、传动轴系及轴承所消耗的功率不能全部测得,制造厂应估算并说明与功率和效率有关的止推轴承、传动轴系及轴承的损失。 对于潜水泵机组的功率测量,应在电缆的引入端进行。所给出的功率和效率应是扣除了电缆和起动器损失的机组本射的功率和效率。 6.5 噪声和振动的测量 泵的噪声和振动测量应分别按GB 10890、GB 10889进行。 7 汽蚀试验方法 汽蚀试验用常温清水进行。以水为介质的汽蚀试验,不能用来精确预测泵在输送非常温清水的其它介质时的汽蚀特性。 7.1 试验类型 汽蚀试验有如下两种不同类型: 一种是仅作校核试验以证明泵在规定的性能和NPSH下运转时能可靠地避免汽蚀,这种试验如本标准7.1.1条所述。 另一种是通过减小NPSH直至可以测出汽蚀对泵性能的影响。这种试验可以较圆满地测得泵的汽蚀性能,如本标准7.1.2条所述。 7.1.1 在规定的流量和NPSH下的试验 这种试验仅证明泵在规定的性能和NPSH下运转时能可靠地避免汽蚀。 如果对于同一流量点,在较低NPSH下的一次试验得出与规定NPSH下试验相同的扬程,则可以认为泵满足不发生汽蚀的要求。 7.1.2 确定临界汽蚀余量的试验 通常保持流量等于常数,逐渐降低泵入口压力。改变NPSH值至首级叶轮扬程降低量达(2+K/2)>H%。此时的NPSH即为临界汽蚀余量(NPSH)c。这种试验可以确定在各种偏离规定的NPSH值的情况下泵的特性。 7.2 改变NPSH的方法 可以采用下述方法改变NPSH: a.采用在吸入管路中增加阻力的方法进行。例如,在吸入管路上装设节流阀进行调节(参考图11); 对于节流阀引起的汽蚀,有时可以用串联安装两个或多个节流阀来加以避免;或者让液体通过节流阀后,直接进入一封闭容器或大口径管中来加以消除。容器和管安装在节流阀与泵的入口之间。此时需要设导流片以及用来抽走容器中空气的装置,特别是在低汽蚀余量时。 当节流阀处于半开且与泵入口法兰相距小于12倍入口管径时,必须确保入口的取压孔所在管路是充满液体的。 b.改变自由液面高度。泵从液位可以调节的水池中,必须横截面无节流的吸入管抽吸液体(参考图12); c.设置闭式回路系统。在保证泵扬程或流量不变的条件下,可以改变系统中压力,或通过调节液温改变汽化压力,使泵内发生汽蚀(参考图13)。 出口和入口调节阀中的汽蚀,可能使这种试验较为困难而需要采用特殊的阀。 为了保持需要的温度,须有对回路中的液体进行冷却或加温的装置,而且还须有一个气体分离罐。分离罐要有足够的尺寸,并且要设计得能防止气体被裹挟到泵的吸入液流中去。 如果泵实际用于输送除气水,那么也必须用除气水作汽蚀试验。 如果Q/A>0.25m/s,则罐内需要设置稳流栅。 此处A是罐的横截面积。 图11 汽蚀试验——利用入口节流阀改变 NPSH 图12 汽蚀试验——用调节入口液位方法改变 NPSH 图13 汽蚀试验——利用闭式回路改变 NPSH 注:盘管冷却可以用从自由液面上方注入冷水并放出热水的方法代替之。 7.3 泵的临界汽蚀余量(NPSH)c的测定 试验时可以采用本标准7.2.1~7.2.3条所述的任何一种方法改变NPSH,并可选用表11中任何一种改变参数的方法,本标准推荐采用在试验过程中改变两个调节参数使流量保持恒定的方法。 在泵的工作范围内,应包括小流量点、规定流量点和大流量点3个以上不同流量点进行汽蚀试验。对于采用使流量保持恒定的试验方法时,对每一个流量点应逐渐降低NPSH,不同的NPSH值不宜少于15个,并在试验曲线即将出现断裂的区域应有较密集的试验点。 7.4 测定NPSH的误差限 对B级试验定为实测NPSH的3%或0.15m,取两者中的大者。 对C级试验定为实测NPSH的5.3%或0.2m,取两者中的大者。 当用高温液体或接近临界点的液体做试验时,要特别注意测量误差限。 7.5 汽蚀试验时泵的扬程、流量、转速、轴功率(必要时)和汽化压力的测量 本标准第6章中有关流量、扬程、转速和轴功率测量的各项要求,亦可用于汽蚀试验。如果测试条件不稳定,而需要重复读数时,允许将NPSH的变化量放宽到最大为表6所规定的扬程变化量的1.5倍或0.15m,取两者中大者。 要注意保证: a.流量测量时,汽蚀不致影响流量计的精度; b.在泵吸入管中的测温传感器不会影响入口压力的测量; c.连接处和填料函处不漏气和吸入管路内没有窝存空气的可能性; d.应当按照本标准7.4条的规定,以足够的精度测定进入泵的试验液体的汽化压力。如果汽化压力是根据测得的进入泵的液体温度按标准资料查得的,则应说明温度测量的精度,以便核对是否满足本标准5.4条的规定。 e.水的温度测量应在吸入管路离泵不超过25倍管径处测量。测温传感器的有效部分插入泵吸入管中的深度应不少于吸入管径的1/8。 8 试验结果按规定转速的换算 在与规定转速不符的转速下得到的所有数据均应换算为以规定转速为基准的数据。 如果试验转速与规定转速相差在本标准5.7.4条所述的允许变化范围内,则关于流量Q、气魄程H、轴功率Pa、汽蚀余量NPSH和效率η的测量数据可按下式进行换算: Qo=Q·(nsp/n) (50) Ho=H·(nsp/n)2 (51) Pa0=Pa·(nsp/n)3 (52) (NPSH)co=(NPSH)c·(nsp/n)2 (53) ηo=η (54) 如果试验转速与规定转速相差超过本标准5.7.4条所述的允许变化范围,则有必要另外规定将试验结果换算为以规定转速为基准的数据的计算公式。 9 性能曲线图的绘制 9.1 性能曲线图 9.1.1 泵的性能曲线图应采用图14的形式。横坐标轴上表示流量Q,纵坐标上分别表示扬程H,轴功率Pa和效率η。 9.1.2 根据测定与计算得出数据绘制曲线,曲线应该圆滑。 9.1.3 绘制在如图14形式上的性能曲线应当是规定转速下的性能曲线。 图14 泵性能曲线图 表14 按ΔH/H=(2+K/2)%测定(NPSH)c的方法 装置形式 | 开式池 | 开式池 | 闭式回路 | 闭式罐或 闭式回路 | 开式池 | 开式池 | 闭式回路 | 开式池 | 闭式回路 | 独立改变的 | 入 口 节流阀 | 水 位 | 吸水面 压 力 | 温度 (汽化压力) | 出口节流阀 | 入 口 节流阀 | 罐中压力 | 水位 | 温度 (汽化压力) | 保持不变的 | 出 口 节流阀 | 入口和出 口节流阀 | 入口和出口节流阀 | 入口节流阀 | 流量 | 流量 | 流量 | 流量 | 随调节面改变的 | 扬程 流量 NPSH 水位 | 扬程 流量 NPSH | 扬程 流量 NPSH 在汽蚀 发生后 | 扬程 流量 NPSH 水位 | 出口节流阀(为保持流量不变)扬程NPSH | 扬程NPSH出口节流阀(当声程开始下降时,为保持流量不变) | NPSH扬程出口节流阀 | NPSH 扬程出口节流阀(当扬程开始下降时,为保持注量不变) | 扬程—流量 和扬程—NPSH 曲线 (NPSH)c—流量 曲线 | 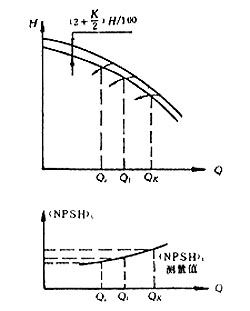 | 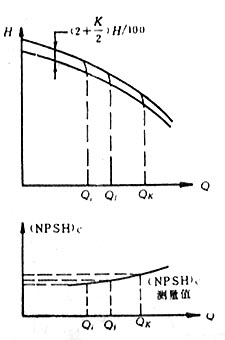 | | 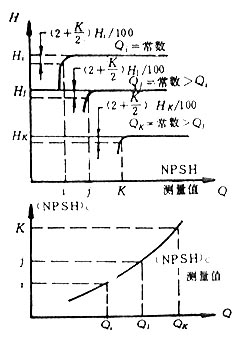 | 9.2 NPSH曲线图 9.2.1 NPSH曲线图应按试验时所用的改变参数的方法分别按表11所示的三种形式绘制。 9.2.2 取H——NPSH曲线上当扬程下降值达到(2+K/2)H/100的NPSH值作为泵的临界汽蚀余量(NPSH)c值。 10 试验的分析 10.1 流量、扬程允差 泵的流量允差为±XQ,扬程允差为±XH。 允差XQ和XH适用于规定性能点Qsp、Hsp。这些允差包括流量Q和扬程H的最大允许总误差限(见表8)和制造允差。 对于B级XQ=0.04 XH=0.02 对于C级XQ=0.07 XH=0.04 如果规定点与试验曲线的垂直距离为±ΔH,水平距离±ΔQ(见图15),则应算出下列的值: (HspXH/QspXQ/Qsp、XQ和HspXH为两半轴的椭圆内。但是,它不可以用来作这样的核对,即对于规定扬程Hsp应该得到一定的流量Q;或是对于规定的流量Qsp,应该得到一定的扬程H,实际上应该注意,检查上面的关系式并不一定意味着下面这种关系成立: 对于规定流量Qsp,扬程H应为:Hsp-HspXH≤H≤Hsp+HspXH 对于规定扬程Hsp,流量Q应为:Qsp-QspXQ≤Q≤Qsp+QspXQ 10.2 效率 规定效率应按照由通过规定性能点QspHsp和QH坐标轴原点的直线与QH曲线的交点所确定的性能点来进行检查。这一点的效率应根据对应的横坐标为Qη曲线上读出。 对于B级试验:交点的效率至少应是规定值的0.972,对机组效率,此值为0.975。 对于C级试验:交点的效率至少应是规定值的0.950,对机组效率,此值为0.955。当试验转速超出本标准5.7.4条规定范围降至50%时,效率应与换算后的规定值(见本标准第8章)相比较。 效率值的差异仅是由于测量误差所致。 10.3 批量生产的定型产品的性能允差 对批量生产的定型产品,其试验性能曲线与标准性能曲线相比较,除规定点的性能允差和效率允差须符合本标准10.1和10.2条要求外,工作范围内其余点的性能允差对C级试验须在下列范围内: 扬程 ±0.06 流量 ±0.08 轴功率 0.08 泵工作范围内其余点的性能分析按式(55)计算后判定,判定方法,同本标准10.1条。 10.4 汽蚀余量 10.4.1 临界汽蚀余量(NPSH)c应小于或等于规定的必需汽蚀余量(NPSH)r。 图15 检查规定点用的QH曲线 附 录 A 水的物理性质 (补充件) 温度 ℃ | 汽化压力 Pa | 密度 kg/m3 | 温度 ℃ | 汽化压力 Pa | 密度 kg/m3 | 0 1 2 3 4 5 6 7 8 9 10 11 12 13 14 15 16 17 18 19 20 21 22 23 24 25 | 610.86 655.97 705.00 756.98 811.99 870.83 933.60 999.30 1069.91 1145.42 1228.78 1313.12 1403.34 1498.37 1599.47 1706.37 1820.12 1934.76 2068.23 2201.60 2334.88 2481.98 2641.93 2815.50 2989.00 3175.41 | 999.80 999.80 999.92 999.96 1000.00 999.98 999.94 999.90 999.84 999.78 999.70 999.60 999.48 999.34 999.20 999.00 998.88 998.72 998.54 998.36 998.20 997.96 997.74 997.54 997.32 997.10 | 26 27 28 29 30 31 32 33 34 35 36 37 38 39 40 41 42 43 44 45 46 47 48 49 50 | 3361.74 3562.68 3775.48 4003.00 4242.28 4496.37 4763.11 5029.86 5322.98 5630.02 5950.71 6284.13 6631.19 7004.93 7378.56 7791.42 8205.26 8645.59 9112.39 9592.82 10099.80 10129.30 11167.90 11741.60 12341.73 | 996.84 996.56 996.30 996.00 995.70 995.36 995.00 994.64 994.26 993.90 993.54 993.20 992.80 992.44 992.20 991.70 991.32 990.94 990.54 990.20 989.74 989.34 988.97 988.52 988.10 | 附 录 B 摩 擦 损 失 (补充件) B1 本标准6.2.1.2条中所给出的计算摩阻所造成的水头损失的公式饮食一个冗长的计算式,但很多情况下计算的结果都不需要修正。 可以利用图B1来预先检查这样的计算是否必要。该图适用于定常圆截面输送冷水的钢质直管,并且假定入口管路和出口管路的管径相同,测量点分别位于离入口法兰和出口法兰两倍管径远的上游和下游处。 如果管径不相同,应取较小的管径作检查。检查时如果图上指出“不需修正”,即可不再进行计算。如果指出“需修正”,则可用图B2求得λ值,不过此图仅适用于输送冷水的钢管。 当管子是其它材料的或输送的液体不是冷水时,可以用图B3所示的莫迪(Moody)曲线确定λ值;或者当用本标准6.2.1.2条中给出的公式计算λ值时,管路粗糙度K的值可以从表B1中查出。 图B1 需要进行损失修正的流速界限指示图 图B2 摩擦系数图 表面粗糙度 k=5.186×10-5m 运动粘度 v=1.022×10-6m2/s 表B1 管的绝对粗糙度K 商品管(新的)材料 | 表面绝对粗糙度 k | mm | 玻璃,拉制黄铜 铜或铝 钢 涂沥青铸铁 镀锌铁 铸铁 混凝土 铆接钢 | 光 滑 光 滑 0.05 0.12 0.15 0.25 0.3~3.0 1.0~10.0 | 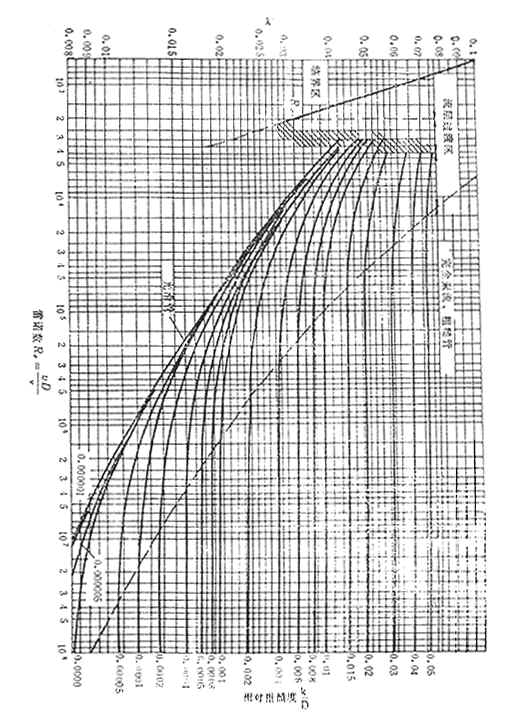 图B3 求摩擦系数λ值的莫迪(Moody)图 附 录 C 泵引起的预旋的影响 (补充件) C1 在小流量工况下,有可能发生预旋,如图C1所示。由于预旋的影响,泵的入口水头的测量将会产生误差。这些误差可以用下述方法检测和修正。 在规定的入口测量截面和较远的上游并确知没有引起的预旋的另一位置(例如泵的吸水池)之间测量出水头差,其值应按流量的二次方规律变化,因此入口总水头H,也应按这一规律变化。相对此规律的任何偏差即表示泵引起的预旋影响的大小。必须用此值来修正入口水头的测量值(图C2的虚线部分)。 图C1 有预旋的装置示例 图C2 实测入口水头的修正 附 录 D 误差的分析和计算方法 (补充件) D1 总则 任何一个测量(例如泵的效率)的不确定度(或误差限),只有通过对所使用的试验装置和设备的一切误差源和影响因素以及所测量的现象的波动和变化进行专门检查才能安全获知。因此,对每一测量都进行这样详细的研究通常是行不通的,而依靠有效的依据并进行分析来估计测量的可靠性则大体上是准确的。最终需要得出的结论是测量所给出的值与试验时的真值两者之差不大可能大于一个固事实上的值,亦即估计出误差绝对值的上界值(即不确定度),或者就估计出一个总误差限。 系统误差和随机误差(或系统不确定度和随机不确定度)均必须加以考虑,同时还应记住,像在泵试验中所遇到的那些不稳定现象的观测结果未必会准确地复现。因此在试验进行之前不能随意预计误差限。 然而,在采用标准装置和校准过的仪表进行泵试验的情况下却可以作出满意的估算。这种估算的基础是预先分析在装置上用类似泵进行的几次试验以确定出可用于各种测量的误差限等级,这样的分析应当遵照本标准附录D(补充件)D2~D5章所规定的方法和步骤进行。在此之后,只要做到总精度是大致每隔一年彻底地检查过的而且测量值的变化不超过本标准5.7.3.2条表6规定的对应于要求测量等级的最大变化容差,应没有必要对所进行的每一试验进行全面分析。因此只要本标准的使用者已确定了他特定试验装置的精度,也就毋需根据本标准5.8条表8的最大总误差限来进行估算。 D2 误差分析 本标准主要涉及在“正常试验状态”下对基本量:扬程、流量、转矩和转速(或轴功率)的测量。 “正常试验状态”指的是在一个试验过程中这些量明显地保持恒定直至为了减小不确定度而有意地改变回路阻力或转速。为了获得泵的特性曲线,根据由若干不同试验条件得到的结果作出扬程、轴功率和效率同流量的关系曲线。对每一试验条件,误差限会有变化。而需要取重复读数的仅是计算误差限被认为是重要的那些点或者当一个读数看来似乎与别的条件下取得的读的趋向不同时。 以上是正常的泵试验方法。本标准附录D(补充件)D4章即是论述这类情况下的每一试验条件的结果不确定度区间的计算方法。 D3 随机误差和系统误差 在实际相同的条件下多次测量同一量时,误差的绝对值和符号的变化时大时小,时正时负,没有确定的规律也不可能预定,但具有抵偿性的误差称随机误差。在同一条件下多次测量同一量时,误差的绝对值和符号保持恒定或在条件改变时按某一确定规律变化的误差称系统误差。 通过多次重复测量并利用概率统计方法处理数据可以减小随机误差,但对系统误差则不起作用,它只有在采用更高精度标准的设备或将同一设备通过校准提高其精度标准时才能减小。不管怎样,系统误差不影响重复观测值的离散程度。 D3.1 随机误差 如果同一量重复观测值围绕一个平均值的弥散是以真正随机方式出现,那么就会有足够多的值按照误差正态分布(或称高斯分布)规律集聚。其他分布规律也有可能,但如没有证据表明是其分布,则将假定随机变量是必然的正态分布。 如果研究同一量几次重复观测的一批读数,其误差呈正态分布,则数值O1,O2,O3,……On,算术平均值为: M=O1+O2+O3+……On/n (D1) 这些观测值的标准偏差为: Sn={(O1-M)2+(O2-M)2+……(On-M)2/n}½ (D2) 当n增加时M值向仪表基本精密度范围内的读数平均其值趋近。如果n足够大,并且变量是正态分布,则可以发现95%的读数将围绕平均值集聚在一事实上的区间内,该区间的大小与式(D2)所给定的标准偏差Sn有关。因此可以认为这些观测值中任一单个观测值落在这些区间内的可能性是95%。这些区间叫95%置之不理信概率的误差限或不确定度。显然99%读数将落在更宽的区间内。该区间也可类似地用Sn表达。不过,对实际的泵试验,由于可靠性足够,普遍采用95%置信概率的误差限,本标准亦是自始至终采用这样的误差限。 通常同一量的少量连续测量值的算术平均值与平均真值的差要比大量连续测量值的算术平均值与平均真值的差大得多。系于n次读数平均值95%置信概率的误差限为: 平均真值 (D3) 其中X是n的函数,给出在表D1中。 表D1 n | 3 | 5 | 7 | 9 | 30 | ∞ | X | 4.3 | 2.8 | 2.5 | 2.3 | 2 | 1.96 | 注:对99%和99.5%置信概率的误差限n=∞时X分别为2.5和3.4。 因此,确定由于试验结果围绕平均值的弥散所致的95%置信概率的不确定度的步骤如下: a.利用式(D1)确定读数平均值M; b.由a得到的M值计算标准偏差Sn; c.将Sn乘以适当的 值。 如此得到的结果将表明在相同条件下得到的100个平均值中有95个可以被期望落在仪表指示平均真值 的区间内。本标准5.7.3.2条的表6即是根据所有测得的和导出的量的最大随机误差限(如表D2所给出的值)而定的。 表D2 | B级 | C级 | 流量、扬程、转矩、轴功率 | ±1.1 | ±2.3 | 转 速 | ±0.35 | ±1.3 | D3.2 系统误差 系统误差主要是由于仪表固有的和结构上的局限性以及仪表较准的局限性和测量方法的不完善产生的。它表现为仪表读数的平均指示值与被测之量的绝对平均真值之间的差异。为了把系统误差控制在适合于各测量等级的一定范围内,本标准对仪表的精度、校准和安装规定了许多条件。各个基本量测量的最大允许系统误差限规定在本标准5.8条表7中。 诸如泵的轴功率,效率等均是导出量。前者由转矩和转速的独立测量值计算得出,后者则由所有被测之量计算之。导出量的系统误差限可以由它们的各个分被测之量的系统误差计算求得(如本标准附录D(补充件)D3.3条所述)。 D3.3 误差的总合 导出量的系统误差限可以通过它的各个线性分量的系统误差按平方规律传播进行总合来计算,例如: 泵效率的百分系统误差限= ±{[转矩 百分系统 误差限] 2+[流量 百分系统 误差限]2+[转速 百分系统 误差限]2+[扬程 百分系统 误差限]2}½ (D4) 一般说,导出量(例如效率)的随机误差限须采用另外方法计算。即首先对每一组读数计算出效率或任何其他导出量的值,然后按标准D3.1条对单项分量所述的完全相同方法计算出效率重复值的标准偏差进而估算其随机误差限,然后就可以用平方规律传播方法将随机误差限与系统误差限相总合,例如: 泵效率的百分总误差限= ±{[效率 百分随机 误差限] 2+[流量 百分系统 误差限]2+[转速 百分系统 误差限]2+[扬程 百分系统 误差限]2+[转速 百分系统 误差限]2}½ (D5) D4 正常试验状态下的误差分析 正常试验状态下重复测量的试验方法在本标准5.7.3.2条中作了规定。如果一批读数中的任何两个读数之间的最大百分差大于本标准5.7.3.2条对9次连续读数所规定的值,则应把试验当作试验条件是不正常的而且超出了本标准的范围来处理。但是如果本标准5.7.3.2条中的条件得到满足,则误差限将小于规定的最大允许误差限。如果系统误差和随机误差按照本标准附录D(补充件)D3章计算的并且如规定的那样进行总合得出基本量和导出量的总误差限,则将得到较窄的误差限。计算的例子可参见本标准附录D(补充件)D6章(例2)。 如果一个量取n次读数并且得到最大值与最小值之间百分差为2d,则它的标准偏差不可能小于: (D6) 并且不可能大于: (对奇数读数) (D7) 困此,只要进行充分分析,就会发现标准偏差落在由式(D6)和式(D7)所给定的两个极值之间。本标准5.7.3.2条表6给出的最大百分允差即是基于式(D7)确定的。因此可以预期得到较按最坏可能分布计算出来的误差限为小的误差限。可是通过全分析得到的误差限减小值对次数少的读数并不大,因此只是在特殊情况下进行复杂的特别分析才是值得的。 D5 误差限的估算 试验所使用的设备和仪表的系统误差将由设备和仪表的校准结果确定。随机误差限可由本标准附录D(被子充件)D3章所给出的最大误差限估算或者如本标准附录D(补充件)D1章所述由与所采用的特定试验装置有关的误差限来估算。估算误差限的例子参见本标准附录D(补充件)D6章。 D6 计算例子 表D3给出的数据即是例1~4的基本计算数据。 表D3 典型的泵试验读数 观测序号 | 转速 r/min | 流量 L/s | 扬程 m | 轴功率 kW | 效率 % | 1 | 1447.5 | 79.88 | 18.70 | 17.64 | 83.00 | 2 | 1447.1 | 79.20 | 18.81 | 17.59 | 83.05 | 3 | 1447.2 | 79.40 | 18.90 | 17.72 | 83.02 | 4 | 1447.4 | 79.48 | 18.75 | 17.60 | 83.01 | 5 | 1447.2 | 79.74 | 18.56 | 17.50 | 82.90 | 6 | 1447.3 | 79.98 | 18.46 | 17.46 | 82.88 | 7 | 1447.1 | 79.59 | 18.71 | 17.60 | 82.97 | 8 | 1447.4 | 79.68 | 18.68 | 17.57 | 83.04 | 9 | 1447.3 | 79.54 | 18.76 | 17.67 | 82.79 | 例1 在可控条件下进行的泵试验结果的分析以保证符合本标准5.7.3.2条表6的要求。 假定上述结果是在本标准5.7.3.2条对重复观测组数所规定的条件下获得的,所有仪表全部满足B级要求。首先取最少的3组读数(序号1~3)计算各个量的最大和最小读数的最大百分差: 转速 略去(小于0.25%) 流量 79.88-79.20/79.88=0.85% 扬程 18.90-18.70/18.90=1.06% 轴功率 17.72-17.59/17.72=0.73% 比较表6可知转速和轴功率满足B级要求,流量和扬程未满足B级但满足C级要求。由于所有被测之量均须全部满足B级要求,故至少还需取两组观测值。如果不出现更大的离散,则将满足B级5次读数的最大百分允差(1.6%)于是取表D3中前5组观测值,其最大差为: 转速 略去 流量 79.88-79.20/79.88=0.85% 扬程 18.90-18.56/18.90=1.79% 轴功率 17.72-17.50/17.72=1.24% 现在只有扬程仍超出B级变化范围,这是由于第5组的读数出现小值。再取两组读数,并对1~7组的观测值作计算: 转速 略去 流量 79.98-79.20/79.98=0.98% 扬程 18.90-18.46/18.90=2.33% 轴功率 17.72-17.46/17.72=1.47% 因为扬程还在7次读数的B级变化范围(2.2%)以外,故再取两组观测值,对1~9组读数进行计算: 转速 略去 流量 79.98-79.20/79.98=0.98% 扬程 18.90-18.46/18.90=2.33% 轴功率 17.72-17.46/17.72=1.47% 此结果与前7组的计算相同,这是由于第8和第9组观测值都未超出前面7组观测值的离散范围。现在,B级9次读数的最大百分允差2.8%已经得到满足。 随后就计算各个被测之量的平均值: 转速:1/9×(1447.5+1447.1+1447.2+1447.4+1447.2+1447.3+1447.1+1447.4+1447.3)=1447.3 流量:1/9×(79.88+79.20+79.40+79.48+79.74+79.98+79.59+79.68+79.54)=79.61 扬程:1/9×(18.70+18.81+18.90+18.75+18.56+18.46+18.71+18.68+18.76)=18.70 轴功率:1/9×(17.64+17.59+17.72+17.60+17.50+17.46+17.60+17.57+17.67)=17.59 效率:1/9×(83.00+83.05+83.02+83.01+82.90+82.88+82.97+83.04+82.79)=82.96 例2 对上述结果详细分析。以计算较窄误差限。 对例1可以作更详细的分析。现以扬程读数为例,对前3次读数取平均值: M=1/3(18.70+18.81+18.90)=18.80 以百分数表示此3个读数为: O1=99.47 O2=100.05 O3=100.53 M=100 由此得: Sn={(100-99.47)2+(100-100.05)2+(100-100.53)2/3-1}½ ={0.532+0.052+0.532/2}½=0.531% 因此系于3次读数平均值的95%置信概率的误差限为: 可以对5、7、9次读数进行类似计算,最后的值为M=18.70,Sn=0.697%。于是  显然,此值在要求的±1.10%(B级)范围内(参见表D2) 例3 测量设备系统误差的计算。 举在现场对照容积箱校冷孔板的例子。 在由例1所给出的平均流量79.61L/s下水银柱差压为651.26mm。校准过程中发现当流量大于48.50L/s时流量计系数实际是常数,在此范围内得到7个系数值: k=3.1225,3.1255,3.1270,3.1300,3.1195,3.1345,3.1180。 其中k 为流量,L/s,h为测得的差压,以mmHg表示。平均k值为3.1255,则各个k测量值以相对平均值的百分数表示为:99.90,100,100.05,100.04,99.81,100.29,99.76。 Sn={(100-99.90)2+(100-100)2+(100-100.05)2+(100-100.14)2 +(100-99.81)2+(100-100.29)2+(100-99.76)2/7-1}½=0.19% 系于7次平均值的95%置信概率的误差限为: 用来作对照校准流量计的容积箱本身应是已经校准过的。在对可能造成误差源的所有诸因素,如计时精度、泄漏和蒸发损失、温度影响等一一加以考虑并按平方规律传播进行总合后,如结果为±0.12%即是95%置信概率的用容积箱测量流量的误差限,则上述k值的相应误差限为: (0.182+0.122)½=±0.22% 在以后使用此流量计时,该误差限即作为系统误差传递。因此,如果表D3列出的流量是用此流量计测得的话,就可以计算出系于9次读数平均值的95%置信概率的总误差限,如例4。 例4 系统误差和随机误差的总合 流量的9次读数平均值为79.61,取此值为100,则其他读数为:100.34,99.48,99.74,99.84,100.16,100.46,99.97,100.09,99.91。 其标准偏差为: Sn={(0.34)2+(0.52)2+(0.26)2+(0.16)2+(0.46)2+(0.03)2+(0.09)2+(0.09)2/9-1}½ =(0.7335/8)½=0.303% 系于流量平均值的95%置信概率的随机误差限 根据例3,系统误差估算为δs±0.22%, 则95%置信概率的总误差限为: 显然,该总误差限在本标准5.8条表8所规定的流量测量最大总误差限(±2.0%)范围内。 附加说明: 本标准由沈阳水泵研究所提出并归口。 本标准由沈阳水泵研究所负责起草。 本标准主要起草人陶耀星。 |